By Dr. Renee Threlfall and Dr. Yue Chen
Research Team: A.L. Gunderman1, J.A. Collins1, A.L. Myers2, R.T. Threlfall2, and Y. Chen1
1Department of Mechanical Engineering and 2Department of Food Science, University of Arkansas, Fayetteville, AR, USA
Fresh-market blackberries are mostly hand harvested to the maintain quality of this delicate fruit from harvest to consumption. Labor shortages, labor costs, and the slow speed of hand harvesting bottleneck potential fresh-market blackberry industry expansion and market-ready supply. Automated harvesting options (shaking the plants, cutting the stems, or using rigid grippers) are used for other fruits. However, these options are not feasible for harvesting fresh-market blackberries because they might cause quality issues such as berry leakage or red drupelet reversion (drupelets turn from black to red) at harvest or during storage.
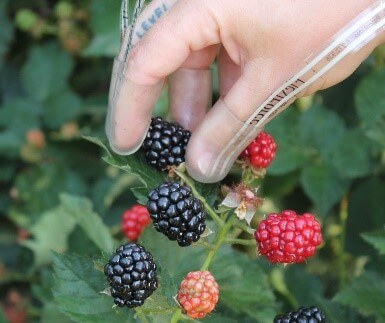
Soft robotics provides a novel option for automatic harvesting by using compliant grippers (rubber, silicone, etc.) that enabling task versatility to grasp and manipulate delicate objects with complex, dynamic shapes. A research team at the University of Arkansas is developing engineering-based solutions using soft robotics to implement delicate harvesting of fresh-market blackberries using a custom-designed soft robotic gripper. One of the first steps to develop the soft robotics gripper is to gather data on harvesting fresh-market blackberries that might be needed to design and program the robot.
When a person harvests a blackberry, what fingers are used to grasp the blackberry, how much force is needed to pick the fruit from the plant, and how does this impact fruit quality? In order to answer these questions, the research team created a custom made, force-sensing apparatus with flexible force sensors on the thumb and index, middle, and ring fingers of a person harvesting fresh-market blackberries (Figure 1). These sensors measured the forces applied during berry harvesting by each finger to the berry surface. The data was recorded for the force-sensing apparatus using a portable water-resistant case housed in a backpack and processed data was transmitted and logged to a mobile work-station (Figure 2).
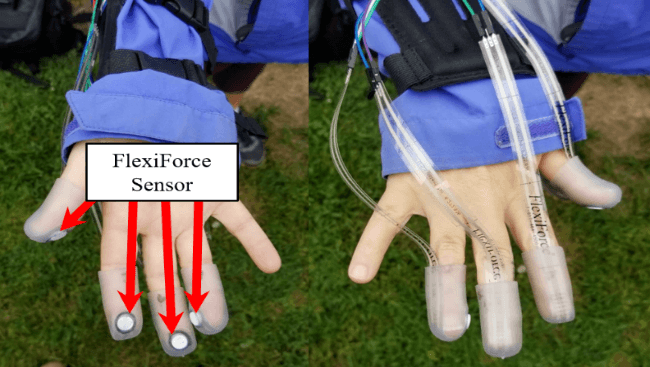
Over 2,000 blackberries were harvested from a commercial blackberry grower in Arkansas using the force-sensing apparatus. Data analysis indicated that the thumb applied the highest force (0.78 N), followed by the middle (0.40 N), index (0.19 N), and ring finger (0.07 N). These results reflect the anatomical relationship of the hand during picking, where the thumb and middle finger act as the primary force applicators while the index and ring finger act as stabilizers. The research team related the measured force values to quality attributes of the blackberries, which were evaluated in clamshells after 21 days at 2°C. The quality attributes were comparable to harvesting without the force-sensing apparatus, with low leakage (6%), decay (<2%), and red drupelets (5%), ensuring the force-sensing apparatus did not compromise berry quality.
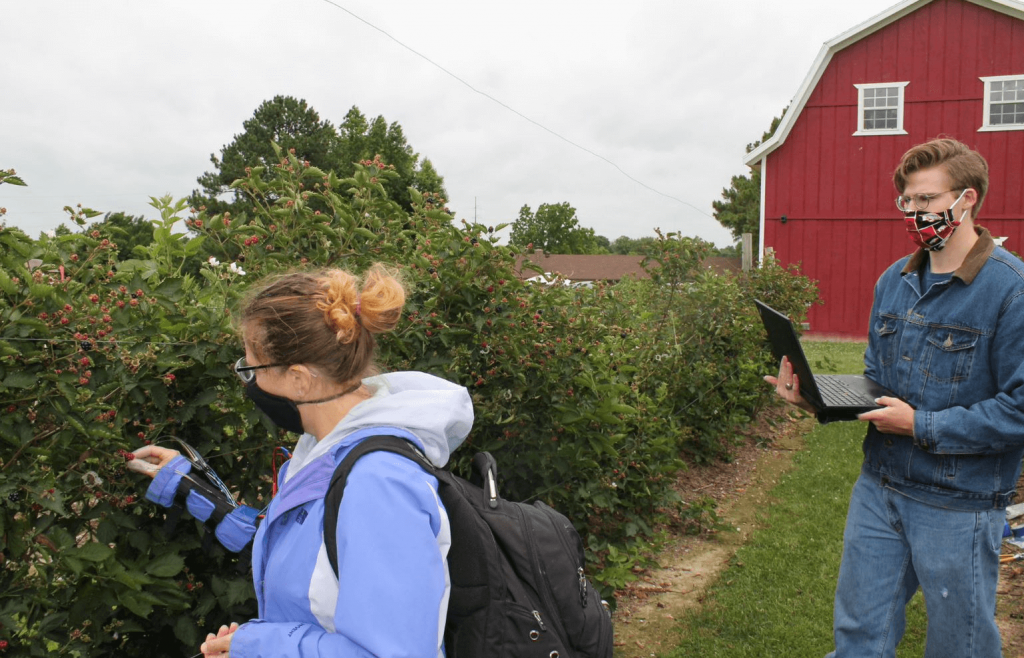
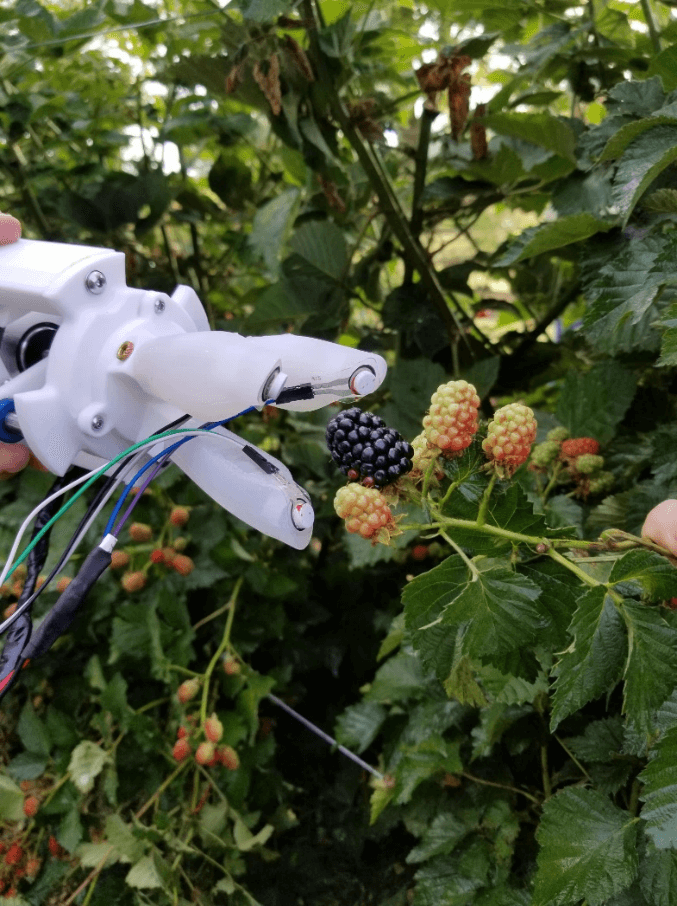
Using these results, a novel, tendon-driven soft robotic gripper was developed using compliant, soft silicone and active force feedback control at the fingertips. The versatile gripper was used to harvest 240 blackberries: 60 berries each at three fingertip force thresholds (0.59 N, 0.69 N, and 0.78 N) and 60 berries as a control with force sensors removed. The blackberries were placed in clamshells as they were harvested (20 berries per clamshell), and their quality attributes were evaluated after 21 days at 2°C. Red drupelets for blackberries harvested with 0.59 N, 0.69 N, and 0.78 N was 0%, 8%, and 16%, respectively, and the control had 0%.
While is it feasible to develop a soft robotic gripper to harvest fresh-market blackberries, more research and development will be needed for commercial implementation. In this research, we were able to determine the number of grippers and the force needed to harvest blackberries with acceptable fruit quality at harvest and during storage. Next, we need to develop robotic perception to find ripe blackberries on the plant for the gripper to harvest and continue evaluations in commercial blackberry farms.
This work has promising potential for soft robotic harvesting of blackberries and lays the foundation for future developments on this gripper. The project team looks forward to working with Arkansas blackberry growers to further evaluate this new soft robotic gripper for harvesting fresh-market blackberries.
Note: This project was funded by University of Arkansas Chancellor’s Innovation Fund grant and an Arkansas Department of Agriculture Specialty Crop Black grant. The project team would also like to acknowledge Sta-N-Step Farm, the location of the 2020 evaluations.